Case Study: Multi-Unit Factory in Weatherford, TX
JD
Introduction
In the heart of Weatherford, TX, a transformative project was undertaken that has set a new standard for storefront installations in multi-unit factories. This case study delves into the intricacies of a successful storefront installation that not only enhanced the aesthetic appeal of the factory but also improved its operational efficiency. This project serves as a beacon for similar industrial upgrades in the region and beyond.
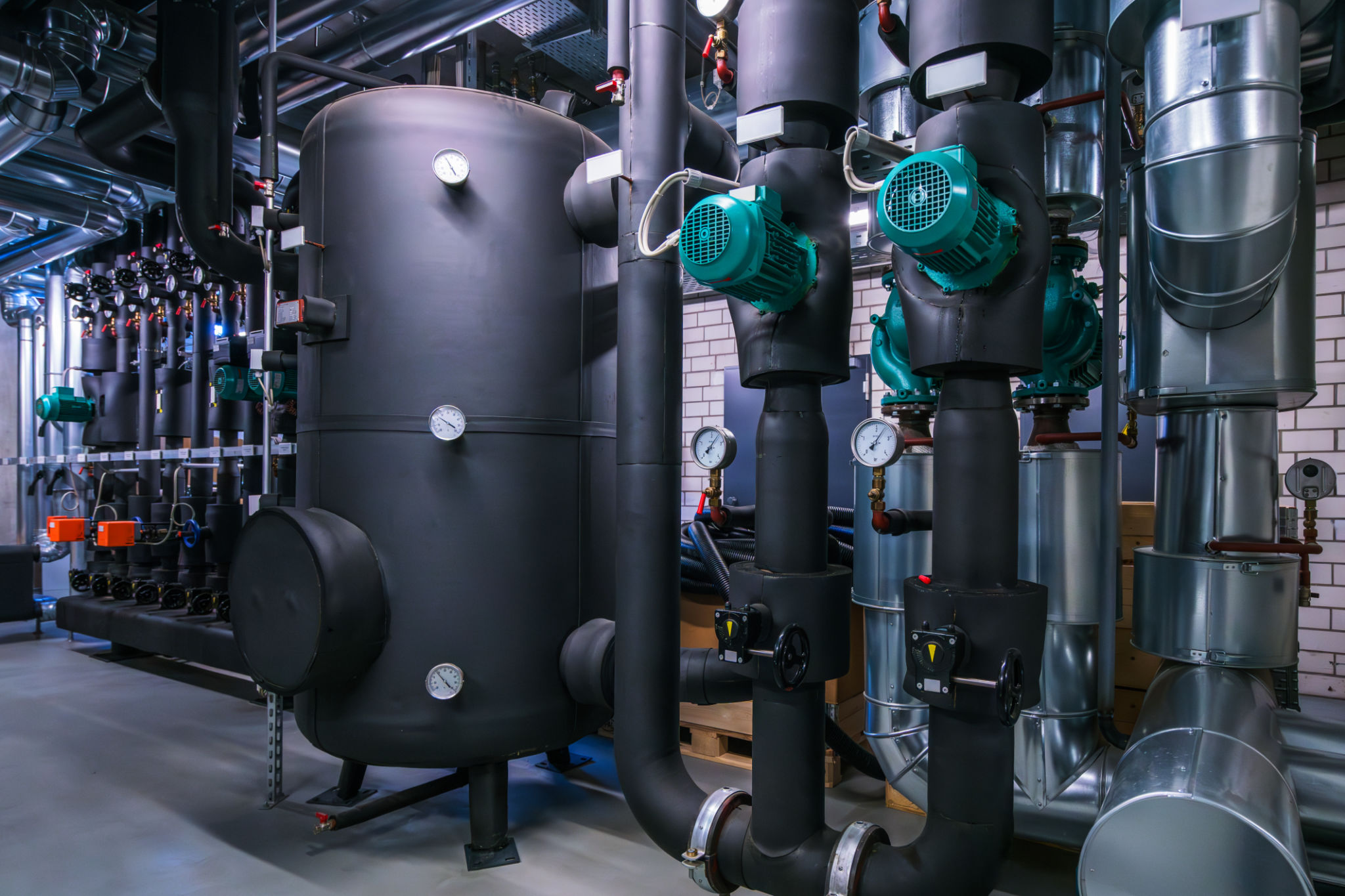
Challenges Faced
Undertaking a storefront installation for a multi-unit factory presents unique challenges. The primary concern is ensuring that the design accommodates the diverse needs of each unit while maintaining a cohesive overall look. Additionally, logistical constraints, such as minimizing disruption to ongoing operations, play a crucial role in the planning phase. Moreover, selecting materials that can withstand the local climate conditions in Weatherford was essential for long-term durability.
Design Considerations
The design team embarked on an extensive consultation process with factory stakeholders to understand their specific requirements. With each unit having unique operational needs, the design had to be versatile yet uniform. A modern, sleek design was chosen to reflect the factory's forward-thinking ethos, incorporating large glass panes to allow natural light to flood the workspaces.
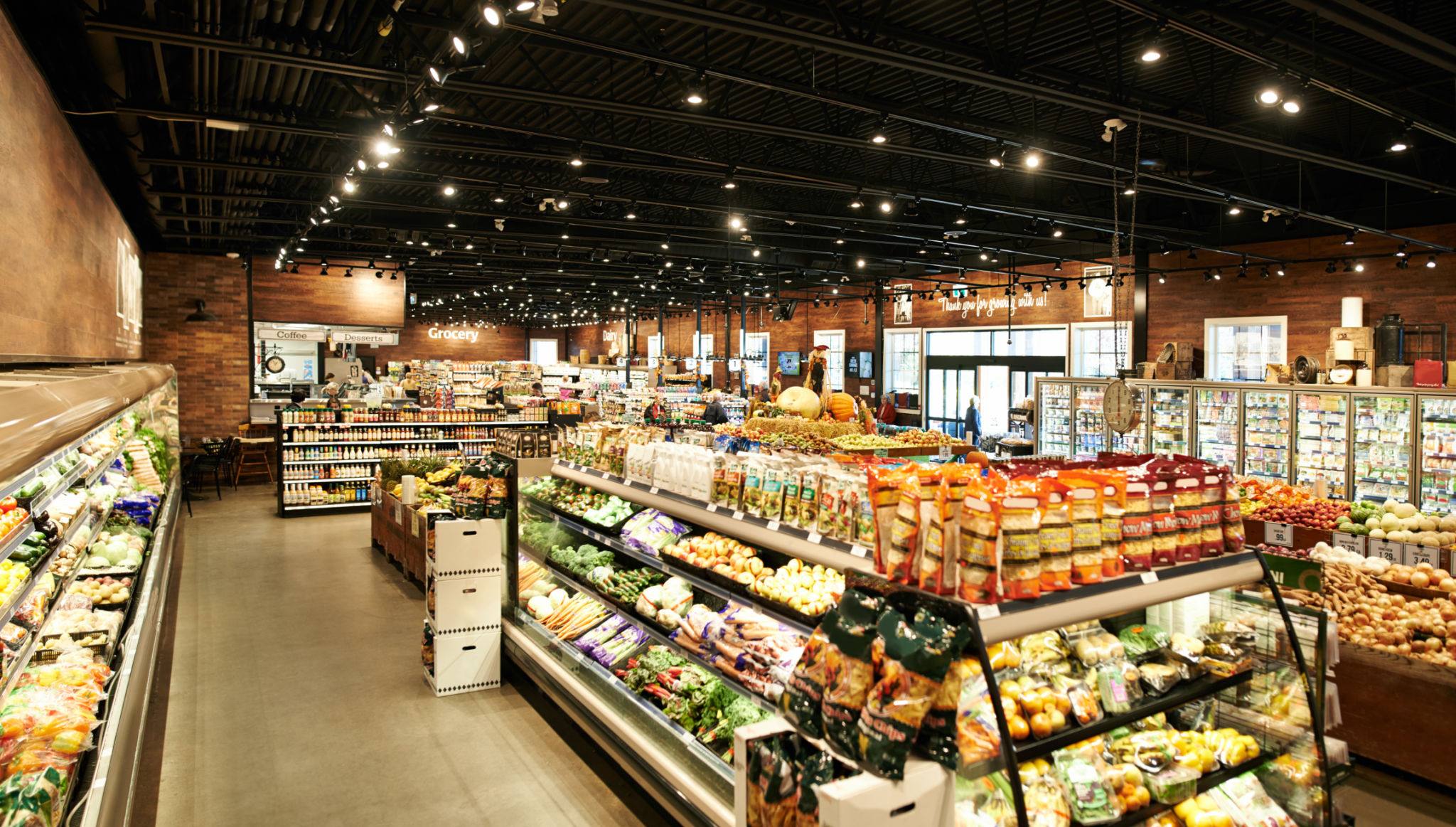
Implementation Strategy
The execution phase was meticulously planned to ensure minimal disruption to factory operations. A phased installation approach was adopted, allowing sections of the factory to remain operational while others underwent transformation. This strategy proved effective in maintaining productivity levels throughout the project duration.
Material Selection
Weatherford’s climate necessitated careful selection of materials to withstand both hot summers and occasional cold snaps. High-quality, energy-efficient glass and aluminum frames were chosen for their durability and thermal performance. This choice not only improved the building's energy efficiency but also contributed to its sophisticated appearance.

Outcomes and Benefits
The completed storefront installation yielded numerous benefits for the factory. The new design significantly improved the facility's curb appeal, attracting potential clients and partners. Furthermore, the increased natural light within the workspaces positively impacted employee morale and productivity.
Environmental Impact
One of the standout features of this project was its positive environmental impact. The energy-efficient materials reduced the factory's overall energy consumption, contributing to lower operational costs and a reduced carbon footprint. This aligns with growing industry trends towards sustainability and energy efficiency.
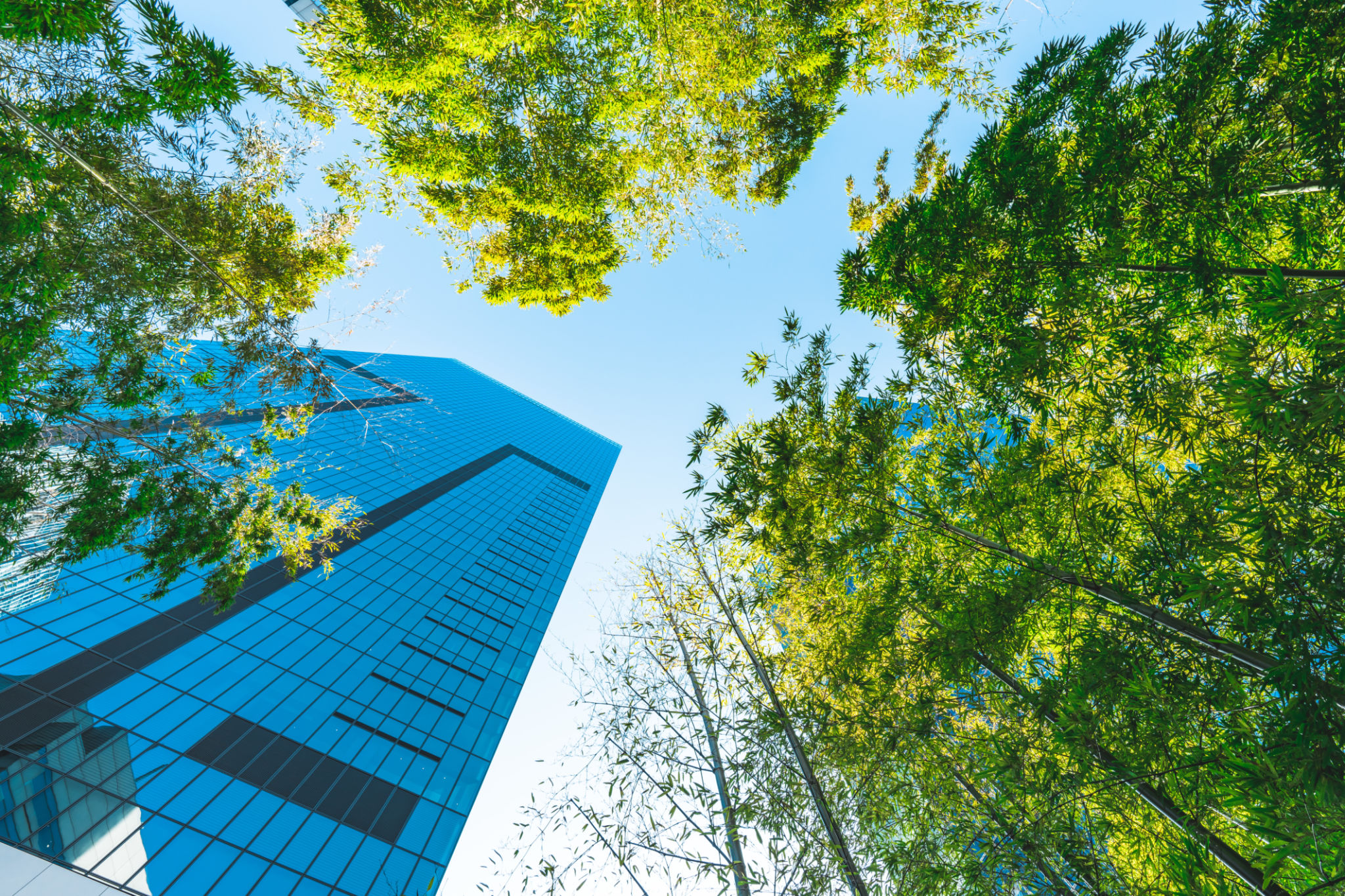
Lessons Learned
This project provided valuable insights into managing complex installations in industrial settings. Key takeaways include the importance of stakeholder engagement in the design process and the benefits of adopting a phased approach to minimize operational downtime. Additionally, selecting materials with long-term environmental benefits proved advantageous.
Future Implications
The success of this storefront installation has set a precedent for future projects in Weatherford and similar regions. It highlights the potential for industrial facilities to combine functionality with modern aesthetics, paving the way for further innovations in industrial design and construction.
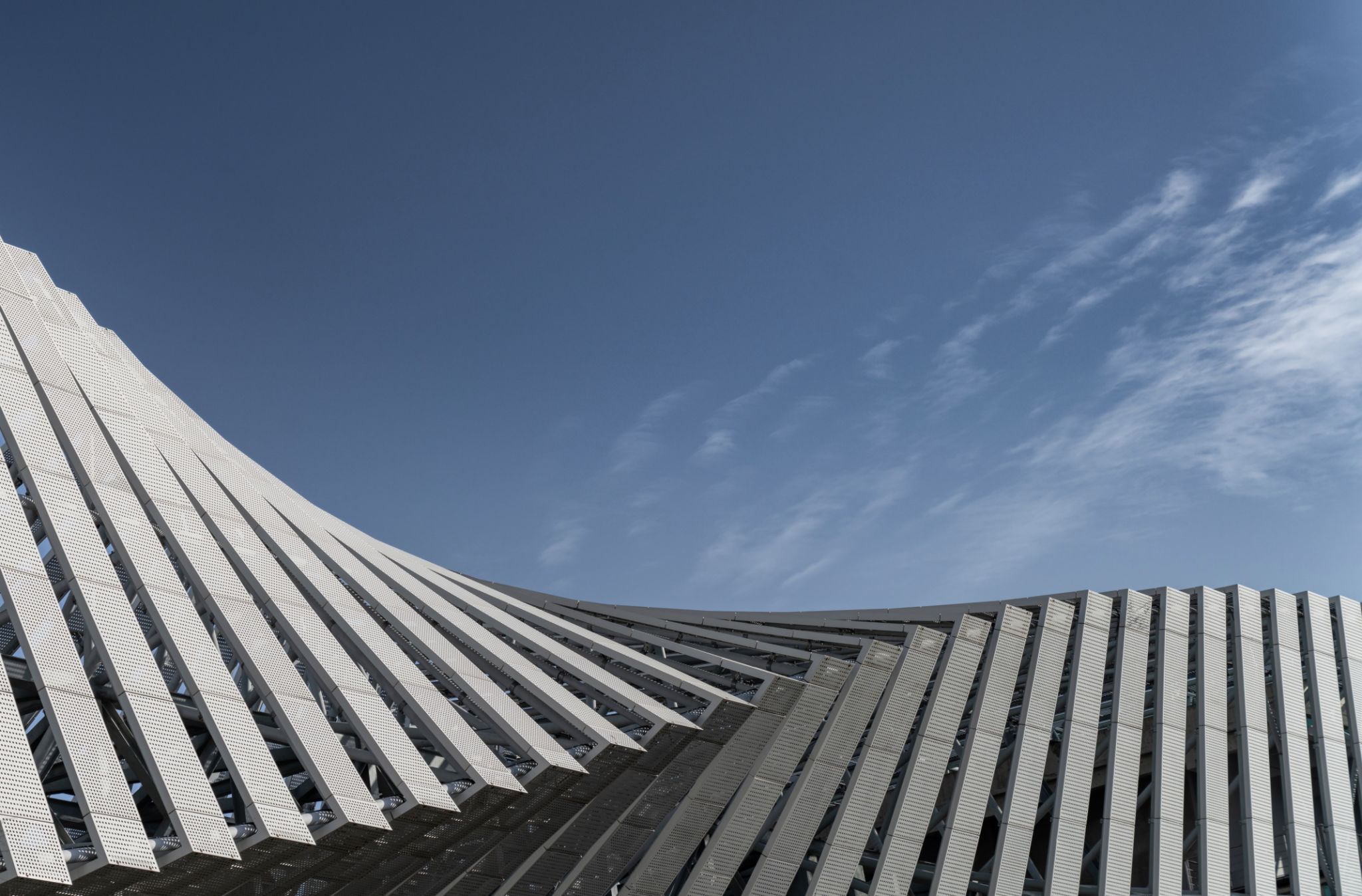